Automation in industries is revolutionizing the way we work and produce goods. From the assembly lines of factories to the intricate logistics of global supply chains, automation is streamlining processes and enhancing efficiency across numerous sectors. This transformation is driven by a continuous evolution of technologies, creating both opportunities and challenges for businesses and workers alike.
The historical progression of automation, from early mechanical devices to sophisticated robotics, has been a significant factor in shaping modern industries. Understanding the diverse types of automation systems and their applications is crucial for navigating this evolving landscape. This exploration delves into the advantages and disadvantages of implementing automation, its impact on the workforce, safety considerations, and future trends.
Introduction to Automation in Industries
Automation in industrial contexts refers to the use of control systems, information technologies, and computer-aided design (CAD) to replace or augment human labor in performing tasks. This encompasses a wide range of technologies and processes, from simple machine controls to complex robotic systems. The overarching goal is to increase efficiency, productivity, and quality while reducing human error and potentially hazardous working conditions.The evolution of automation has been a gradual process, accelerating over time.
Early forms were often focused on repetitive tasks, while modern automation integrates across numerous industrial processes, from manufacturing to logistics and beyond. The development and application of automation technologies have significantly reshaped industrial landscapes.
Historical Evolution of Automation
Automation’s journey is marked by a series of technological advancements. Early forms of automation, dating back to the Industrial Revolution, involved mechanical devices like automated looms and power-driven machinery. These innovations were initially focused on increasing output in textile production.
Early Automation Technologies and Impact
The introduction of programmable logic controllers (PLCs) in the mid-20th century was a pivotal moment. PLCs allowed for more complex control systems in manufacturing, enabling the automation of sequential processes and enhancing efficiency. The use of robots, initially in automotive assembly lines, showcased the potential for increased speed and precision.
Current State of Automation Technologies
Modern automation technologies are characterized by their integration and sophistication. Computer numerical control (CNC) machines allow for precise machining and intricate part production. Advanced robotics, including collaborative robots (cobots), are increasingly integrated into diverse industrial settings, handling tasks from material handling to assembly and inspection.
Automation Capabilities in Modern Industries
The capabilities of modern automation technologies extend beyond simple repetitive tasks. These technologies facilitate real-time data collection and analysis, leading to improved process optimization and predictive maintenance. Advanced machine learning algorithms are increasingly used to identify patterns and predict potential issues, leading to proactive maintenance and minimizing downtime. This approach is being used in sectors such as manufacturing, logistics, and even healthcare.
Examples of Automation in Action
The application of automation varies widely across industries. In manufacturing, automated assembly lines ensure consistent product quality and high throughput. In logistics, automated guided vehicles (AGVs) optimize material handling, streamlining distribution networks. These are just a few examples of the impact of automation on the modern industrial landscape.
Types of Automation: Automation In Industries
Industrial automation encompasses a wide spectrum of technologies, each tailored to specific tasks and industry needs. Understanding these diverse approaches is crucial for evaluating their applicability and effectiveness within different operational contexts. From simple, repetitive tasks to complex, integrated systems, automation technologies are continually evolving to enhance efficiency, productivity, and safety in various sectors.
Categorization of Automation Systems
Automation systems are often categorized based on the level of human intervention and the degree of intelligence incorporated. This categorization allows for a structured understanding of the various automation approaches. Different levels of automation provide varying degrees of autonomy and control, impacting the complexity and cost of implementation.
- Programmable Logic Controllers (PLCs): PLCs are essential components in automation systems, acting as the brain of automated processes. They are programmed to control machinery and equipment based on predetermined instructions. This type of automation is particularly well-suited for discrete manufacturing processes where the steps involved are relatively fixed and can be easily programmed. PLCs are widely used in assembly lines, robotic systems, and various industrial applications requiring real-time control.
- Industrial Robots: Industrial robots are automated manipulators programmed to perform a range of tasks. They are particularly valuable for repetitive or hazardous operations, increasing efficiency and reducing human error. Their ability to perform precise and consistent movements makes them crucial in tasks such as welding, painting, material handling, and assembly.
- Computer Numerical Control (CNC) Machines: CNC machines utilize computer-aided design (CAD) and computer-aided manufacturing (CAM) technologies to perform precise manufacturing tasks. These machines are programmed with instructions for intricate operations, including cutting, drilling, and shaping. CNC technology is commonly employed in industries requiring high precision and customization, such as aerospace and automotive manufacturing.
- Supervisory Control and Data Acquisition (SCADA) Systems: SCADA systems are sophisticated systems that monitor and control large-scale processes in real-time. These systems are integral to industries with continuous processes, like power generation, water treatment, and oil refining. They provide real-time data analysis and allow for remote control of the process, enhancing efficiency and safety.
- Automated Guided Vehicles (AGVs): AGVs are self-propelled vehicles that navigate predetermined paths within a factory or warehouse. They are often used for material handling, transporting goods between different workstations, and improving overall logistics. Their efficiency is notable in large-scale operations requiring consistent movement of materials.
Comparison Across Industries
The choice of automation type significantly depends on the specific industry and the requirements of the production process. For example, the automotive industry heavily relies on industrial robots and CNC machines for high-volume production, while the food processing industry often utilizes automated systems for precise ingredient handling and packaging.
Automation Type | Applications | Advantages |
---|---|---|
PLCs | Assembly lines, robotic systems, and industrial automation | Real-time control, cost-effectiveness, and adaptability to various tasks |
Industrial Robots | Welding, painting, material handling, and assembly | High precision, consistency, and reduced human error in hazardous operations |
CNC Machines | Aerospace, automotive, and other industries requiring high precision and customization | High precision manufacturing, intricate designs, and reduced production time |
SCADA Systems | Power generation, water treatment, and oil refining | Real-time monitoring, remote control, and enhanced safety in large-scale processes |
AGVs | Material handling and logistics in factories and warehouses | Efficient material transportation, reduced manual labor, and improved operational flow |
Benefits of Automation in Industries
Automation in various industries is driving significant economic, social, and environmental transformations. This shift, while presenting challenges, offers substantial advantages across the board, impacting workforce composition, production efficiency, and sustainability. The benefits extend beyond simple cost reduction to encompass improved safety, reduced environmental impact, and enhanced product quality.
Economic Advantages
Automation often leads to substantial cost reductions in industries. Reduced labor costs, coupled with increased output and efficiency, create significant financial advantages for companies. For instance, automated assembly lines in automotive manufacturing can produce vehicles at a faster pace and lower unit cost, thus increasing profitability. Moreover, automation allows for 24/7 operation, maximizing production capacity and generating higher revenue streams.
This continuous operation translates into substantial gains in return on investment, especially in industries with high production demands. The ability to adapt to fluctuating demands also becomes more efficient and flexible.
Social Benefits
Automation, while potentially displacing certain roles, can also create new and higher-skilled jobs. Workers previously engaged in repetitive tasks can transition to roles involving design, maintenance, or oversight of automated systems. This shift in the workforce necessitates retraining and upskilling programs to equip employees with the necessary skills for these emerging roles. The transition is often gradual and requires a proactive approach by both companies and educational institutions to bridge the skills gap and support a smooth transition for employees.
Environmental Benefits
Automated processes can lead to significant environmental improvements. Minimized waste, optimized resource utilization, and reduced emissions from machinery are just some examples. In manufacturing, automated systems can precisely control the use of raw materials, minimizing waste and maximizing yield. Smart factories, equipped with advanced sensors and automation, can optimize energy consumption and reduce their overall carbon footprint.
Automation in industries is rapidly changing the landscape, and that extends beyond just production lines. Companies are increasingly looking at sustainable practices, like using Eco-friendly fashion brands for their supply chains. This shift towards environmentally conscious choices is a key component of future-proofing industrial operations.
This is particularly important for industries with high energy consumption, helping them to operate more sustainably and responsibly.
Impact on Workforce Composition and Skill Requirements
The implementation of automation necessitates a change in workforce composition and skill requirements. While some jobs may become obsolete, new jobs emerge requiring different skill sets. The workforce needs to be adaptable and proactive in acquiring the skills necessary to operate and maintain automated systems. This includes proficiency in areas like data analysis, programming, and advanced technology.
The development of new technical skills, coupled with a focus on adaptability, is key to a successful workforce transition in the face of increasing automation.
Comparison of Manual and Automated Processes, Automation in industries
Feature | Manual Process | Automated Process | Cost Savings | Efficiency Gains |
---|---|---|---|---|
Labor Cost | High | Lower (maintenance and supervision) | Potentially significant | Higher |
Production Rate | Lower | Higher | Potentially significant | Significant |
Product Quality | Variable, susceptible to human error | Higher consistency, reduced error | Potential reduction in rework costs | Higher |
Safety | Potentially hazardous | Reduced risk of injury | Reduced worker compensation costs | Higher |
Flexibility | High | Moderate to High (with appropriate programming) | Potential increase in setup costs | Higher, depending on automation level |
The table above highlights the key differences between manual and automated processes, showcasing the potential for substantial cost savings and efficiency gains through automation. The specific benefits and drawbacks will vary depending on the industry and the nature of the automation implemented.
Challenges of Implementing Automation
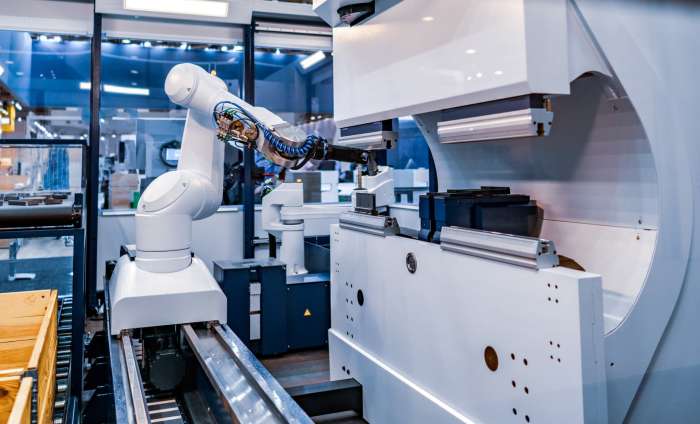
Implementing automation in industries, while offering numerous benefits, presents significant challenges. These challenges often involve careful planning, resource allocation, and adaptation to new technologies and work processes. Understanding these hurdles is crucial for successful automation initiatives.
Integration with Existing Processes
Integrating automation technologies into existing industrial processes can be complex. Legacy systems, differing protocols, and incompatible software may necessitate substantial modifications to existing infrastructure. Furthermore, the need for retraining personnel and restructuring workflows adds to the complexity of the transition. A thorough assessment of existing systems and careful planning for seamless integration are critical for mitigating these challenges.
Cost Considerations
Implementing and maintaining automation systems involves substantial upfront and ongoing costs. Initial investment in hardware, software, and installation can be considerable. Training personnel, troubleshooting, and potential downtime also contribute to the total cost. Ongoing maintenance, repairs, and upgrades further increase the long-term expenditure. Careful budgeting and cost analysis are essential to ensure that the financial benefits of automation outweigh the associated expenses.
For instance, a factory replacing its entire assembly line with robotic arms might need to allocate millions of dollars for new equipment, programming, and training.
Technical and Logistical Hurdles
Automation projects frequently encounter technical and logistical hurdles. These can include difficulties in programming complex automated systems, ensuring reliable communication between different components, and managing data flow and storage. Supply chain issues, delays in component delivery, and scheduling conflicts can also impact the project timeline and budget. Furthermore, finding skilled personnel to design, implement, and maintain the automation system can be a significant hurdle.
The complexity of integrating various components can result in unexpected issues, requiring extensive debugging and troubleshooting. For instance, a failure in one component of a complex automated assembly line can lead to delays and significant production losses.
Safety Concerns
Automated systems pose unique safety concerns that must be addressed. Ensuring that workers are protected from potential hazards, such as moving machinery, laser beams, or harmful chemicals, is paramount. The implementation of safety protocols, including emergency shut-off mechanisms, safety fences, and worker training, is critical. For example, a robotic arm in a manufacturing plant needs to have appropriate safety guards to prevent workers from being injured during operation.
Regular safety inspections and maintenance are essential to ensure the continued safe operation of automated systems. The potential for accidents or equipment malfunctions must be thoroughly considered and appropriate safety measures must be implemented.
Automation in Specific Industries
Automation is transforming various industries, driving efficiency, productivity, and safety improvements. This section delves into the specific applications of automation across key sectors, illustrating its impact and showcasing practical examples.
Automation in the Automotive Industry
The automotive industry heavily relies on automation for its manufacturing processes. Sophisticated robotic systems are crucial for tasks like welding, painting, and assembly. Automated guided vehicles (AGVs) transport parts and components throughout the factory, optimizing material flow. Computer-aided design (CAD) and computer-aided manufacturing (CAM) software play a significant role in designing and manufacturing vehicles, increasing accuracy and reducing errors.
This integrated automation leads to higher production rates, reduced labor costs, and improved product quality.
Examples of Automation in the Manufacturing Sector
Automation plays a pivotal role in enhancing efficiency and precision in the manufacturing sector. Automated guided vehicles (AGVs) and conveyor systems are used to transport materials between different stages of production. Robotic arms perform repetitive tasks, ensuring consistency and minimizing human error. Automated storage and retrieval systems (AS/RS) manage inventory, ensuring optimal stock levels and reducing downtime.
These examples highlight the widespread adoption of automation in modern manufacturing, boosting productivity and reducing production costs.
- Automated material handling systems: These systems use robots and conveyor belts to move materials efficiently and accurately through various production stages. This ensures materials are in the right place at the right time, minimizing delays and maximizing output.
- Automated quality control systems: Automated inspection systems, often employing vision-based technologies, identify defects and anomalies in products, ensuring high quality standards. This helps reduce waste and rework, improving overall production efficiency.
- Automated packaging systems: These systems automate the process of packaging finished goods, ensuring consistent and efficient packaging for distribution.
Automation in the Food Processing Industry
Automation in the food processing industry is crucial for maintaining consistent product quality and safety, while handling high volumes of production. Automated systems can perform tasks such as sorting, packaging, and labeling, minimizing human interaction and reducing potential contamination risks. Temperature control systems are vital for maintaining optimal conditions during various stages of processing. Automation plays a crucial role in meeting the demand for food products, ensuring hygiene and maintaining consistent product quality across large production volumes.
- Automated sorting systems: These systems use optical and sensor technologies to sort products based on size, shape, or other criteria. This precision ensures only high-quality products proceed to the next stage.
- Automated packaging lines: These lines automate the process of packaging food items, minimizing contamination risks and ensuring consistent product presentation. Automated systems also increase packaging speed and reduce labor costs.
- Automated processing equipment: Robotic arms and other automated equipment perform tasks such as slicing, dicing, and mixing ingredients, maintaining precise consistency across large batches.
Automation in Logistics and Supply Chain Sectors
Automation is transforming logistics and supply chain management, significantly improving efficiency and reducing costs. Automated guided vehicles (AGVs) are used to transport goods within warehouses and distribution centers, optimizing material flow and reducing manual handling. Automated storage and retrieval systems (AS/RS) help manage inventory, optimizing storage space and minimizing retrieval time. These automation implementations improve the speed and efficiency of the entire supply chain.
- Automated warehousing systems: These systems combine automated storage and retrieval systems (AS/RS) with robots and conveyor systems to automate material handling, storage, and retrieval within warehouses. This improves order fulfillment and reduces manual labor.
- Automated transportation systems: Automated vehicles, such as autonomous trucks and drones, are increasingly used for transporting goods across longer distances. This reduces transportation costs and improves delivery times.
- Automated order fulfillment systems: These systems automate the process of picking, packing, and shipping orders, improving order accuracy and reducing processing time. This reduces errors and increases efficiency.
Automation and Safety
Automated systems, while offering significant advantages in industrial settings, demand meticulous attention to safety protocols. Integrating safety measures into the design and operation of automated equipment is paramount to minimizing risks and maximizing worker well-being. Robust safety procedures are not merely a legal requirement but a critical component of a successful and sustainable automation strategy.Implementing comprehensive safety protocols in automated environments is crucial for preventing accidents and maintaining a safe working environment.
The integration of safety features into automated equipment ensures that potential hazards are mitigated, and workers are protected from harm. A proactive approach to safety fosters a culture of responsibility and empowers workers to recognize and respond to potential risks effectively.
Automation in industries is rapidly evolving, with new technologies constantly emerging. Considering the increasing use of wearable tech, like smartwatches, in various professions, a good understanding of features like battery life and processing power is crucial. For a detailed breakdown of key factors to consider when purchasing a smartwatch, check out our comprehensive Smartwatch buying guide.
This ultimately helps professionals stay connected and productive while on the job, boosting overall efficiency in automated processes.
Importance of Safety Protocols
Safety protocols are indispensable in automated systems to prevent accidents, safeguard personnel, and maintain operational integrity. These protocols encompass a wide range of measures, from physical barriers and emergency shutdown systems to rigorous training programs for operators. A robust safety culture promotes a proactive approach to risk management, minimizing the likelihood of incidents and maximizing worker well-being.
Safety Measures in Automated Environments
Various safety measures are implemented in different automated environments to mitigate risks and ensure worker safety. These include:
- Physical Barriers: Automated systems often incorporate physical barriers, such as fences, cages, and light curtains, to prevent unauthorized access to hazardous areas and protect workers from moving parts or machinery. These barriers serve as a critical first line of defense against potential accidents.
- Emergency Stop Systems: These systems are essential for quickly halting automated processes in case of emergencies or malfunctions. Operators must be readily trained to utilize these systems effectively and efficiently, ensuring swift responses to critical situations.
- Sensors and Monitoring Systems: Sensors and monitoring systems play a crucial role in detecting anomalies and potential hazards in real-time. These systems provide continuous surveillance of automated processes, triggering alerts and safety protocols in case of deviations from pre-defined parameters. This proactive monitoring minimizes the risk of accidents by detecting problems before they escalate.
Enhancing Worker Safety Through Automation
Automation can significantly enhance worker safety by reducing human exposure to hazardous tasks and environments. Automated systems can handle tasks that are physically demanding, repetitive, or dangerous for human workers. By transferring these tasks to machines, automation minimizes worker fatigue, reduces the likelihood of injuries, and promotes a safer working environment. Moreover, automation enables data collection and analysis to identify potential hazards and optimize safety procedures.
Safety Protocols for Various Automation Systems
The following table Artikels safety protocols for various automation systems.
Automation System Type | Safety Protocols |
---|---|
Robotics | Enclosed workspaces, safety sensors, emergency stops, and robot programming to avoid collisions. |
Automated Guided Vehicles (AGVs) | Navigation systems with obstacle detection, visual sensors, and emergency stop systems to prevent collisions. |
Automated Material Handling Systems | Safety interlocks, emergency stops, and programmable logic controllers (PLCs) to control the movement of materials and prevent accidents. |
Automated Warehousing Systems | Laser scanners, safety lighting, and emergency shutdown mechanisms to protect workers from falling objects or collisions. |
Automation and Sustainability
Automation is no longer solely about increased productivity and efficiency; its role in achieving sustainability is increasingly recognized. Integrating automation with environmentally conscious practices is vital for the long-term health of industries and the planet. By optimizing resource use and minimizing environmental impact, automated systems can contribute significantly to a more sustainable future.
Optimizing Resource Use with Automation
Automation technologies are capable of significantly optimizing resource utilization in various industrial settings. By precisely controlling processes, automated systems can reduce waste, minimize energy consumption, and improve overall resource efficiency. This involves optimizing production schedules, adjusting machinery parameters based on real-time data, and implementing closed-loop control systems that regulate material flow and energy usage.
Reducing Environmental Impact in Industrial Processes
Automation plays a crucial role in minimizing the environmental footprint of industrial processes. Automated systems can facilitate the adoption of cleaner technologies, optimize energy consumption, and reduce the generation of hazardous waste. Real-time monitoring and control capabilities inherent in automation enable proactive responses to potential environmental issues, minimizing disruptions and promoting sustainable practices.
Sustainable Automation Technologies
Several technologies exemplify the integration of automation with sustainability goals. Advanced robotics, equipped with sensors and AI, can handle complex tasks with minimal human intervention, improving efficiency and reducing waste. Smart manufacturing systems, using IoT and data analytics, optimize energy usage and material flow, leading to lower environmental impacts. For example, automated guided vehicles (AGVs) can transport materials within a facility more efficiently than manual methods, reducing fuel consumption and emissions.
Environmental Benefits of Automation
The environmental benefits of automation are multifaceted and impactful. Reduced resource consumption leads to lower energy bills and reduced reliance on raw materials, contributing to a lower carbon footprint. Minimized waste generation translates to decreased pollution and improved environmental quality. Improved process control can lead to reduced water usage and reduced emissions of harmful substances. For instance, automated systems in water treatment plants can optimize water purification processes, reducing the need for extra chemicals and improving overall efficiency.
Automated systems in the food industry can reduce food waste through precise inventory management and optimized storage conditions. These are just a few examples demonstrating how automation can contribute to a more sustainable industrial landscape.
Future Trends in Industrial Automation
Industrial automation is rapidly evolving, driven by advancements in technology and the need for increased efficiency and productivity. This transformation is reshaping industries across the globe, leading to innovative solutions and new possibilities. The future of industrial automation promises to be even more integrated and sophisticated, leveraging cutting-edge technologies to address complex challenges and unlock unprecedented opportunities.The future of industrial automation will be characterized by greater integration and intelligence.
Automation systems will become more interconnected, sharing data and coordinating actions across various stages of production. This interconnectedness will facilitate real-time decision-making, predictive maintenance, and optimized resource allocation, ultimately leading to increased efficiency and reduced operational costs.
Emerging Technologies
The landscape of industrial automation is being reshaped by a confluence of emerging technologies. These advancements are transforming traditional automation practices and opening new avenues for innovation. Key among them are artificial intelligence (AI), machine learning (ML), the Internet of Things (IoT), and robotics.
Artificial Intelligence (AI) and Machine Learning (ML)
AI and ML are revolutionizing industrial automation by enabling systems to learn from data, adapt to changing conditions, and make autonomous decisions. These technologies empower automation systems to perform tasks previously requiring human intervention, such as quality control, predictive maintenance, and process optimization. Examples include AI-powered quality inspection systems that identify defects with high accuracy and ML algorithms that predict equipment failures, enabling proactive maintenance and minimizing downtime.
The Internet of Things (IoT)
The increasing connectivity of industrial equipment via the IoT is transforming the way industries collect, analyze, and utilize data. IoT-enabled sensors and devices collect real-time data on machine performance, environmental conditions, and operational parameters. This data is then used to optimize processes, predict maintenance needs, and improve overall efficiency. A tangible example of this is the use of IoT sensors in manufacturing plants to monitor equipment health and predict potential failures, leading to reduced downtime and improved productivity.
Advanced Robotics
Advanced robotics are becoming increasingly sophisticated and capable of performing complex tasks. Collaborative robots (cobots), for instance, are designed to work alongside human operators, augmenting their capabilities and enhancing safety. Examples include cobots in assembly lines that handle delicate parts, increasing speed and accuracy while minimizing human risk.
Impact on Industries
The integration of these technologies will have a profound impact on various industries. Manufacturing will see greater automation in production processes, leading to increased output and reduced labor costs. Logistics and supply chains will benefit from autonomous vehicles and optimized routing algorithms, improving efficiency and reducing transportation costs. Furthermore, industries such as healthcare and agriculture will see increased automation in tasks such as surgery and crop monitoring, improving outcomes and productivity.
Automation and Sustainability
The integration of automation with sustainability is becoming increasingly important. Automated systems can optimize resource consumption, reduce waste, and improve energy efficiency, contributing to a more sustainable future. This can manifest in automated systems in factories that optimize energy usage based on real-time demands, reducing energy consumption and lowering carbon footprint.
Case Studies of Successful Automation Implementations
Industrial automation has proven its transformative power across various sectors. Successful implementations often showcase not only the technological advancements but also the crucial aspects of planning, execution, and adaptation. These case studies offer valuable insights into the benefits and challenges of automation, providing lessons learned that can be applied to future projects.
Automotive Manufacturing
The automotive industry has been a pioneer in adopting automation. A successful example involves a major automaker implementing robotic welding and painting systems. This significantly increased production output, reduced labor costs, and improved product quality by minimizing human error. Challenges included the initial high investment cost and the need for extensive training for employees to operate and maintain the new machinery.
The lesson learned here is that careful planning, encompassing budget allocation, workforce retraining, and potential production disruptions, is crucial for a smooth transition.
Warehouse Logistics
Automated guided vehicles (AGVs) and robotic picking systems have revolutionized warehouse operations. A major e-commerce company successfully deployed AGVs to transport goods within their warehouse, dramatically improving order fulfillment speed and reducing errors. This increased efficiency and reduced labor costs. However, the implementation faced challenges related to integrating the new systems with existing infrastructure and ensuring seamless data flow.
The crucial lesson learned was the importance of thorough system integration and robust data management to ensure the full potential of the automation is realized.
Food and Beverage Processing
Automation is also transforming the food and beverage industry. A large food processing plant implemented automated sorting and packaging lines, which led to a considerable increase in output and a substantial reduction in packaging material waste. The automation also improved the consistency of product quality and reduced the risk of contamination. Challenges included the need to adjust existing workflows to accommodate the automated systems and to ensure compliance with strict food safety regulations.
A key takeaway is the importance of rigorous validation and testing to ensure automation adheres to stringent industry standards.
Pharmaceutical Manufacturing
The pharmaceutical industry demands stringent quality control. A pharmaceutical company implemented automated quality control systems, reducing errors and improving the consistency of drug production. This also allowed for faster production cycles, which is crucial in the fast-paced pharmaceutical industry. Challenges included the high cost of implementing sophisticated automation systems and the necessity of stringent validation procedures to ensure regulatory compliance.
The lesson learned underscores the importance of careful cost-benefit analysis, coupled with thorough regulatory compliance to navigate the complexities of the industry.
Table of Case Study Summaries
Industry | Automation Implementation | Key Benefits | Key Challenges | Lessons Learned |
---|---|---|---|---|
Automotive | Robotic welding and painting | Increased production, reduced costs, improved quality | High initial investment, training needs | Thorough planning crucial for transition |
Warehouse Logistics | Automated guided vehicles (AGVs) | Faster order fulfillment, reduced errors | System integration, data flow | Comprehensive system integration vital |
Food and Beverage | Automated sorting and packaging | Increased output, reduced waste, consistent quality | Workflow adjustments, safety regulations | Validation & testing crucial for compliance |
Pharmaceutical | Automated quality control | Reduced errors, consistent drug production, faster cycles | High implementation costs, validation procedures | Cost-benefit analysis and regulatory compliance paramount |
Ethical Considerations of Automation
The increasing adoption of automation in industries presents a range of ethical dilemmas. Careful consideration of these issues is crucial to ensure responsible implementation and maximize the benefits while mitigating potential harms. Automation systems, while often designed to improve efficiency and productivity, can also raise concerns about worker displacement, potential biases, and the overall impact on society.The development and implementation of automation systems must be approached with a commitment to ethical principles.
This includes considering the potential consequences for workers, the environment, and society as a whole. A proactive and thoughtful approach can help ensure that automation serves humanity’s best interests.
Worker Safety and Well-being
Ensuring the safety and well-being of workers is paramount when implementing automation. Automation should enhance, not diminish, worker safety. Automated systems should be designed to minimize risks associated with hazardous tasks and provide a safe working environment. This includes incorporating safeguards and emergency protocols, and offering appropriate training and support to workers to adapt to new roles and responsibilities in an automated environment.
Potential Biases in Automated Systems
Automated systems are trained on data, and if that data reflects existing societal biases, the system can perpetuate and even amplify those biases. For instance, if a facial recognition system is trained predominantly on images of one demographic, it may perform less accurately or exhibit bias against other demographics. This can have significant implications in areas like hiring, loan applications, or even criminal justice.
Addressing potential biases requires careful data curation, algorithm design, and ongoing monitoring to ensure fairness and equity.
Responsible Development and Implementation
Responsible development and implementation of automation necessitate a holistic approach. This includes: proactive engagement with workers and communities to address concerns, thorough assessments of potential societal impacts, and ongoing evaluation and adaptation of systems to mitigate unintended consequences. Continuous monitoring and adjustments to ensure the ethical integrity of automated systems are critical. The integration of ethical considerations throughout the automation lifecycle is essential.
This proactive approach emphasizes fairness, transparency, and accountability in the development and deployment of automated systems.
Addressing Worker Displacement
Automation can lead to job displacement, potentially impacting the livelihoods of workers in certain industries. However, this does not necessarily imply a negative outcome. Automation can also create new job opportunities in areas like system maintenance, programming, and data analysis. Reskilling and upskilling initiatives are crucial to support workers in adapting to the changing job market. Government policies and industry partnerships can play a critical role in fostering a smooth transition for workers affected by automation.
Conclusive Thoughts
In conclusion, automation in industries is a multifaceted phenomenon that presents both significant benefits and potential challenges. The integration of these technologies demands careful consideration of economic, social, and ethical implications. By understanding the nuances of automation, from its historical context to its future potential, businesses and workers can better adapt to this evolving landscape and leverage the opportunities it presents.
FAQ Corner
What are the primary economic benefits of industrial automation?
Automation often leads to increased productivity, reduced labor costs, and improved output quality. This can translate to significant cost savings and higher profitability for businesses.
How does automation impact workforce composition?
Automation can displace some jobs, particularly those involving repetitive tasks. However, it also creates new roles requiring specialized skills, such as automation engineers and maintenance technicians.
What are some key safety protocols in automated systems?
Safety protocols in automated systems are critical and include measures such as physical barriers, safety sensors, emergency shut-off mechanisms, and rigorous training for operators.
What are some ethical considerations surrounding automation?
Ethical considerations include ensuring fair labor practices, preventing bias in automated systems, and addressing potential job displacement through reskilling initiatives.